Key Safety and Health
Management Activities
Safety as a core value, KOLON ENP actively
promotes safety culture activities to achieve this.
-
01 BBS (Behavior Based Safety)
A program aimed at preventing accidents by identifying unsafe behaviors of workers associated with accidents and inducing safe behaviors, rather than machinery defects or the environment.
-
02 An Innovation Campaign for Safety Culture
Through participatory programs such as firefighting competitions and safety quizzes, it focuses on raising awareness of safety among all employees to create an experiential safety culture.
-
03 Responsibility-Led Safety Inspection
A system where responsible individuals and decision-makers lead regular safety inspections and improvements. Through this, we can prevent accidents in advance and create a swift and safe working environment.
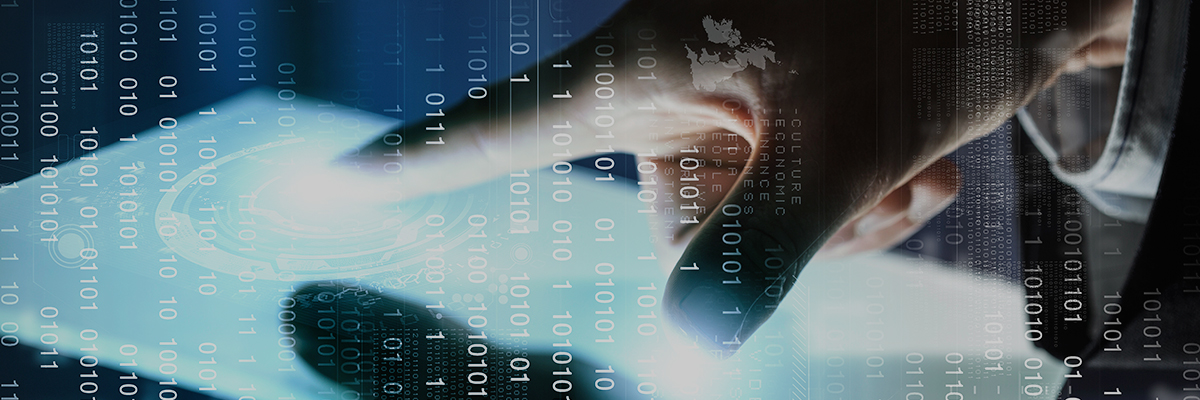
IPAS
-
Intelligent Proximity Alert System
-
To prevent forklift accidents which can be a high risk of a major accident, an advanced forklift safety system called IPAS (Intelligent Proximity Alert System) based on Ultra-Wideband (UWB) technology has been introduced.
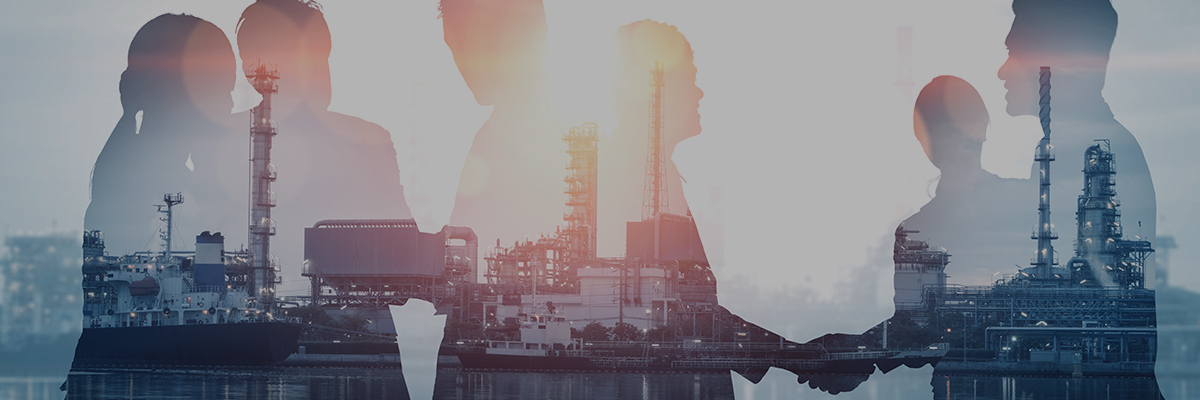
Safety and Health Incentive System
-
We encourage voluntary safety and health culture formation by actively rewarding employees who participate in safety and health activities and demonstrate outstanding performance.
-
01 Excellent Safety Practice Employee Rewards
We operate a system to select and certify employees who have shown outstanding performance in safety management every half-year and reward them.
Through this program, we aim to foster a voluntary safety culture, enhance accident prevention, demonstrate safety leadership, and improve safety levels. -
02 Open it, the ideas to prevent accidents
When employees propose ideas to prevent accidents, outstanding ideas are selected and implemented after evaluation.
We are making efforts to proactively prevent accidents through this process.
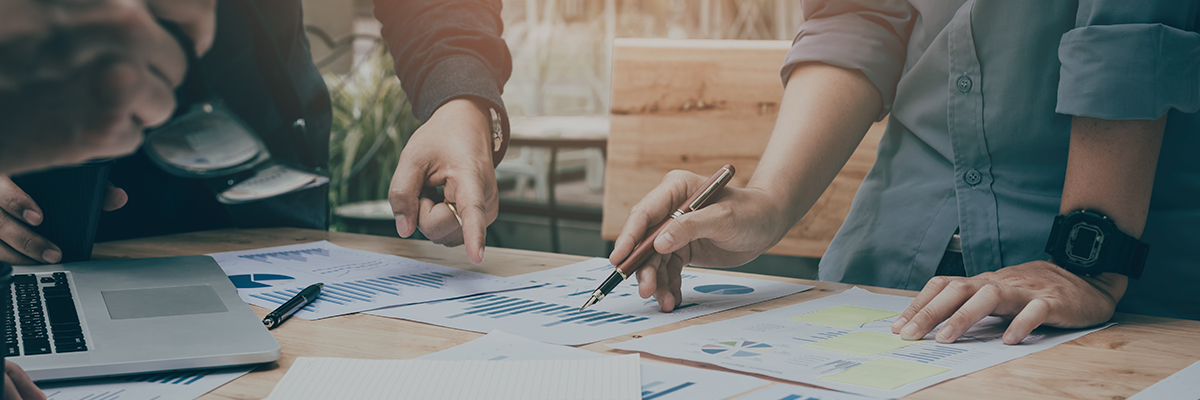
Dedicated Safety and Health Improvement Activities
-
01 Operation of the ESH Upgrade Committee
Every month
It shares the status of safety and health management across the organization, discusses safety and health issues, and strives to improve safety management levels. -
02 Risk Assessment
Factory risk assessments (1 time / 1 year)
Task risk assessments (1 time / 1 year)
Process risk assessments (1 time / 4 years) -
03 Preventive Safety Diagnostics
Collaborative process safety diagnostics with experts
Establishment of safety management supervision checklists and regular checks
Monitoring of compliance issues
Collaborative safety assessment with global leading safety culture companies
Organization and operation of an in-house safety diagnostic team -
04 Operation of PSM & Chemical Accident Prevention Management Plan System
Operation of process safety management and special management of chemical accidents
-
05 Safety and Health Management Policy CEO Reporting and Approval
Safety resolutions and conferences
Propose safety slogans and catchphrases
Establishment of safety and health execution policies.